HOME » FUTA-Q Technology » Interview by Kyoto Prefecture
Interview by Kyoto Prefecture
Interview by Kyoto Prefecture
update :
Ryozo Futaku, the president of FUTA-Q, took the interview by Kyoto Prefecture Office, the article being posted on the company Introduction page in the Kyoto Prefecture’s website.
Interviewer: Mr. Ashikaga of the Manufacturing Promotion Division in Kyoto Prefecture Office Posted date on the Kyoto Pref.’s website: March 29, 2018
The first Introduction of the femto-second laser in Kyoto
【Mr. Ashikaga】
You have introduced a femto-second laser machine. I know that laser processing can be used for removing process such as hole making, joining process such as welding, or modifying process. And there are various kinds of laser media including CO2 gas, fiber or YAG laser in solid state, and semiconductor laser. First of all, please begin with the overview of laser machines.
【Futaku】
The CO2 laser is playing a major role among laser processing machines and is used most widely for sheet metal working. It processes a work by applying heat to it with infrared ray having long wave length, whereas fiber laser has several tens of times stronger laser intensity with the same average laser radiation-power because of its small spot diameter. The YAG laser, YAG being the acronym of the elements of the media, is suitable for welding metals as well as widely used in the medical industry. The semiconductor laser is used in consumer products, information equipment, or dental devices for its low energy consumption and low manufacturing price.
【Mr. Ashikaga】
When it comes to femto-second, femto- means one thousandth of pico- which means one thousandth of nano- which means one thousandth of micro- which means one thousandth of a second. Is it right?
【Futaku】
Right. The femtosecond laser machine utilizes ultrashort pulse having the pulse width, or the irradiation time of laser, of femtoseconds. One femtosecond is one quadrillionth of one second. A light, which can travel 300,000 kilometers in one second, can travel only 0.3 micrometer in one femtosecond.
【Mr. Ashikaga】
Hard to imagine, isn’t it? What’s the benefits of it?
【Futaku】
The laser intensity is proportional to the energy which is inversely proportional to the spot area and the pulse width of the laser beam. Therefore, femtosecond laser has tremendous large energy-intensity although the total amount of the energy is not so large, because the pulse width is compressed to the femtosecond range. It is the first benefit that it can process in high precision of sub-microns to microns with the energy compressed in terms of time and space.
【Mr. Ashikaga】
That makes sense.
【Futaku】
Unlike CO2 laser or YAG laser which is used for ordinally processing, a femtosecond laser does not utilize the heat for processing. In the process of CO2 laser or YAG laser, the material melts or evaporates by the thermal energy converted from the energy of the molecules which vibrate by absorbing the laser energy, while in the femtosecond laser processing, the molecules are instantly removed by being cut the bond with the intense thermal energy before the heat is diffused into the work. This means, which is the second benefit, that femtosecond laser can process not only metals but resins, even materials which have low melting points and is easily affected by heating.
【Mr. Ashikaga】
It’s amazing.
【Futaku】
The fact that the heat cannot be conducted enough to the surrounding area gives us the third benefit that the circumference of the processed area has less damages like cracks.
【Mr. Ashikaga】
Femtosecond laser machines are rarely found in other companies, aren’t they?
【Futaku】
In Kyoto, FUTA-Q is the first company that installed the machine except for universities. A three-dimensional laser machine is especially novel one even in universities.
【Mr. Ashikaga】
What is your intention of this introduction?
【Futaku】
We could contribute to development of preventive medical cares and low invasive treatments, or reduction of medical cost through the development of next generation catheters. In such a way, we like to establish the method for application of micro-precision machining to respond a wide range of needs. Furthermore, we will be commissioned by other companies in Kyoto to draw businesses into Kyoto, resulting in the contribution to the community.
【Mr. Ashikaga】
Your company is now leading the business utilizing femtosecond laser machine which has just started even at the nationwide level.
By the way, I’ve heard that the number of employees will excess 200 in forthcoming April. I look forward to your business expansion.
Supporting global companies by designing and developing core mechanism units.
We will directly support global companies by designing and developing core mechanism units.
【Mr. Ashikaga】
Your company marked the 100th anniversary of your founding. You are already famous for β-titanium, but would you explain about your business here again?
【Futaku】
We are producing various parts and β-titanium pipes throughout the year. The parts are used for a wide range of industries, which include ones for medical devices such as forceps, stents, and needles, for various analyzers or industrial equipment, for leisure articles like fishing rod tops, and for commodities like plastic screws for eyeglasses. The total number of the item types is over 5,700 in a year.
【Mr. Ashikaga】
That’s awesome, isn’t it?
【Futaku】
We have now more than 170 employees who are working in Headquarters, Kyoto Factory including R&D center, and Yagi Factory, other than sales offices in Tokyo and Germany. We are working on processing smaller and more precise parts every day to meet our clients’ requirements. I believe that they see us as something that could be the last stronghold who can surmount challenges the other companies tend to avoid. We are now focusing on helping our clients by designing and developing their core mechanism units as well as just processing or assembling.
【Mr. Ashikaga】
Could you explain it a little further?
【Futaku】
Our company began the business in 1917 to process metals for making Buddhist instruments such as Buddhist bells, and candle stands. We now employ more than 170 various talented workers who have a wide range of expertise like unique processing techniques accumulated for many years. All these things including our employees and our business network are now supporting our strength which are our state-of-the-art technology, large item small scale production, and problem-solving skills. By combining our human resources and structural assets, we have built the support group that help our clients at an early stage of product development before drawings or detail specifications are fixed.
【Mr. Ashikaga】
You are expanding your market into Europe and India now, which makes me uneasy about difficulties in the business.
【Futaku】
We are directly doing businesses with large or global companies in medical, analysis, or industrial equipment industry both domestic and overseas. They are fortunately running their business on a similar basic rule. Having market-oriented policy, we will continue to provide our state-of-the-art technologies.
World’s best inner-surface polishing technology for small pipes
【Mr. Ashikaga】
Will you talk about the company’s features in technical aspect?
【Futaku】
First of all, we are doing business in various fine processing using a wide range of technologies such as machining, rare metal wire producing, laser processing, laser welding, mirror surface finishing, inner surface polishing, and surface treatment. For example, we produce a titanium medical part with the minimum diameter of 0.32 mm by shaving-out. Our laser processing can process various kinds of materials. Our unique technique can also remove the dross (burr-like welded material attaching to the opposite surface to the working surface) which is generated by laser cutting to make a clean surface.
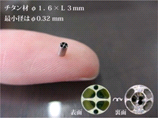
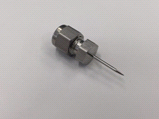
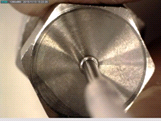
Left: Titanium medical part
Middle: Needle welded by laser with needle body
Right: Welded area having clean surface
【Mr. Ashikaga】
I see.
【Futaku】
Furthermore, we can apply inner polishing to a small pipe having the minimum diameter of 0.1 mm. This polishing process with polishing agent or wire can make a pipe having a low surface roughness and a high circularity to suppress the accumulation of contaminations ultimately. The surface treatment including plating or Teflon-coating with the thickness of 1 micron or less is also available in accordance with the purpose of usage. I believe that we have one of the best techniques for this process in the world.
The world’s first in-house integrated-manufacturing of β-titanium pipes
【Mr. Ashikaga】
That’s great.
【Futaku】
In addition to that, we are producing β-titanium pipes in the world’s first integrated-manufacturing line in-house, which covers from raw-pipe making by rolling to processing it according with the purpose of usage.
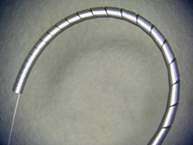
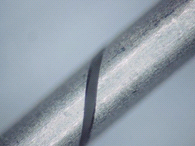
The photo on the right: Enlarged view of the area processed by laser, which enable the pipe to be manipulated flexibly.
【Mr. Ashikaga】
It is amazing that β-titanium can withstand the weight of a car, and has the restoration performance for its original shape and more rusting resistance than stainless steel, despite of its lightness like a feather.
【Futaku】
We developed this product for responding to our client’s earnest wish of a blood analyzer nozzle having non-flexibility and rusting resistance. In general, β-titanium tends not to be favored to be used because of its difficult-working property with galling or burning. On the contrary, taking notice of its uncommon strength, corrosion resistance, and restoration performance, we have developed the world’s first in-house integrated-manufacturing system for β-titanium small pipe with the outer diameter of 0.5 mm and the inner of 0.3 mm. It took as long as 10 years to establish the whole system.
ZEN (ultra-lightweight β-titanium foldable wheelchair) and the non-destructive inner surface inspector
【Mr. Ashikaga】
You also developed ZEN, the ultra-lightweight β-titanium foldable wheelchair.
【Futaku】
This foldable type chair has the equivalent strength to a fixed type wheel chair due to its ultra-lightweight frame made of β-titanium. The height and tilt angle of the seat surface is user-adjustable by having the modular structure.
【Mr. Ashikaga】
You have invented the inner surface roughness tester for a small pipe, haven’t you?
【Futaku】
For measuring the inner surface roughness of a final pipe product, there has been no other ways but cutting it open. This tester measures the air pressures of the inlet and outlet of a pipe to determine the inner roughness non-destructively. I am sure that this will be useful for both manufactures and our clients.
【Mr. Ashikaga】
Can you talk about your future plans?
【Futaku】
Yes, we have a lot of plans. For example, we would like to enforce the development of products combining a metal and another material such as glass or resin. Furthermore, we will introduce more femto-second laser machines to provide more sophisticated processes.
【Mr. Ashikaga】
That must be something to look forward to.
【Futaku】
Forty percent of our clients’ orders are in small lot of one to five. I believe that we can manufacture existing parts at lower cost by utilizing the knowhow obtained from our large-item small-scale production. We will keep going forward toward the next 100 years.
【Mr. Ashikaga】
I can feel your company culture of openness and trusting relationship while the company keeps growing. I can also touch the essence of your management spirit from “FUTA-Q Spirit in ABCDE”.
【FUTA-Q Spirit in ABCDE】
Assume a good luck.
Be cheerful.
Cherish good connections.
Dream big.
Enhance your will.